CMMS Software
Find the best CMMS Software for your organization. Compare top similar Software systems with customer reviews, pricing and get a free demo.

Asset Infinity
By PcsInfinity
Features: Asset Management Service Management
Platforms Deployments Business Size Mid-Market, Enterprise, Goverment
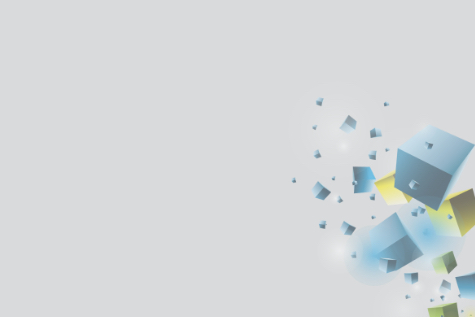

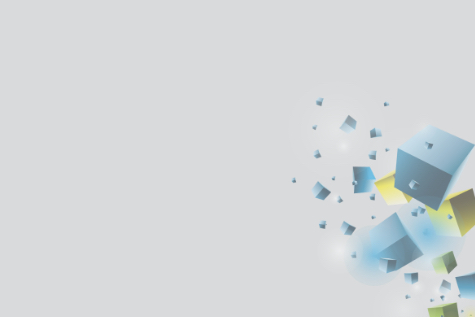
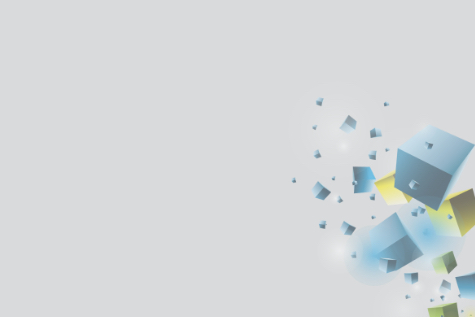
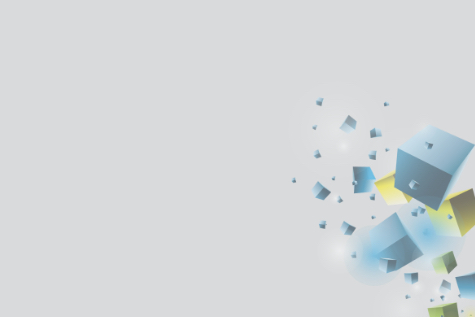
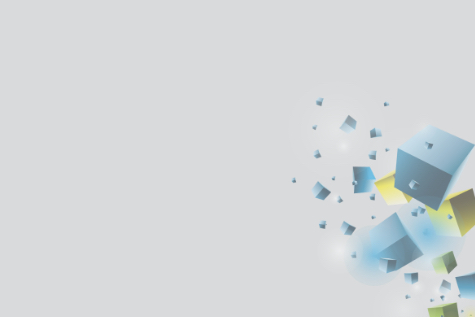
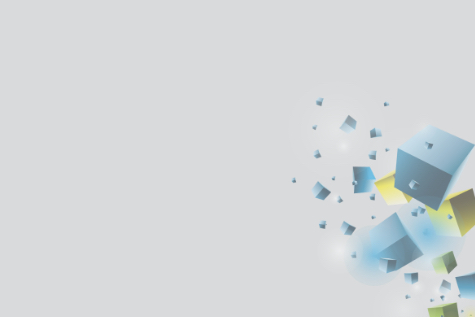
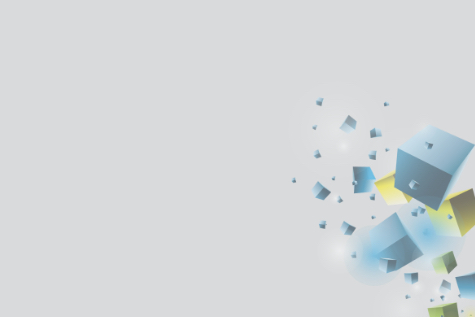
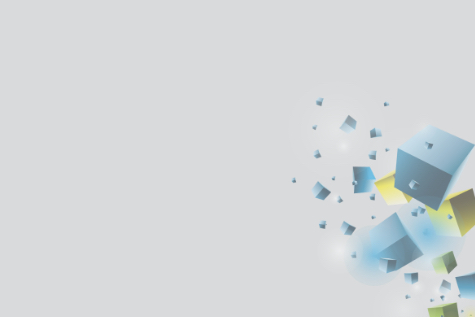
FaciliWorks CMMS
By CYBERMETRICS CORPORATION
Features: Asset Management Module Major Asset Event Tracking
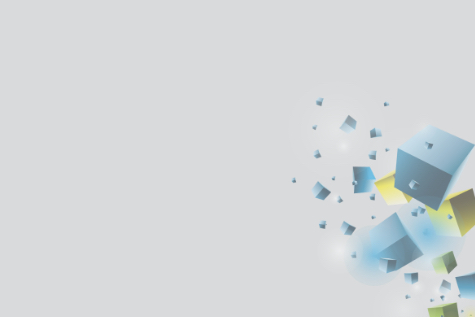
CMMS Software Buyers Guide
- What is CMMS Software?
- What are the Ideal Features of CMMS Software?
- What are the Different Types of CMMS Software?
- What are the Issues Faced While Using CMMS Software?
- What are the Benefits of CMMS Solutions?
- What are the Trends in CMMS Software?
- How Much Does CMMS Solutions Cost?
- Why Purchase CMMS Software from WareBuy?
-
What is CMMS Software?
-
A CMMS (or computerized maintenance management system) software assists companies plan, measure, track, and optimize everything to do with maintenance on a digital platform. The software help companies manage and organize inventory, assure the safety of inventory, conduct preventive maintenance tasks, and more. To better understand what a computerized maintenance management software is, here is complete breakdown of the term into each individual component:
- Computerized: This refers to the fact that your maintenance data is saved on a computer. Earlier, maintenance data was mostly recorded manually because of which maintenance was hugely reactive instead of proactive. Maintenance was carried out only when an issue occurred. Preventive maintenance was not common since it was impractical to track which assets required frequent maintenance when all the maintenance records of your assets were kept on paper. With the emergence of CMMS solutions, companies shifted to computers from pencil-paper. Organizations could quickly generate accurate reports, track work orders, and instantly decide which of their assets needed preventive maintenance. This resulted in improved organization, extended asset lifespans, and eventually increased profits and lowered costs.
- Maintenance: Maintenance is what CMMS software users do daily, whether it is performing daily inspection on a generator or responding to an on-demand work order for a broken asset. Normal computer solutions cannot perform the work of a skilled technician. However, what it can do is make sure tasks are correctly prioritized and that everything works smoothly (labor, inventory) to ensure success. CMMS software offers technicians the freedom to concentrate more on hands-on maintenance and less on paperwork.
- Management: Managing maintenance is the most vital role of a CMMS software. Maintenance management solutions are developed to offer users instant insight into the state of their maintenance requirement with accurate inventory forecasts, comprehensive work order schedules, and immediate access to countless invaluable reports. Computerized maintenance management software solutions make maintenance management simpler by empowering managers with valuable data so that they can make the informed decisions.
- System: A system is a combination of capabilities and features inside a CMMS. Multiple CMMS software provides different kinds of systems. The best CMMS software systems are the ones that let users to accomplish their maintenance goals more efficiently while offering time-saving features that result in efficient time management and reduction of costs.
-
What are the Ideal Features of CMMS Software?
-
Analyzing and choosing the top CMMS software can be a difficult task. There are some important features that must be checked for when choosing a CMMS software. The software gathers and stores data about scheduled maintenance and equipment repairs, as well as maintains an inventory of parts and materials. These solutions also keep track of associated costs and handles all related workflows. Here are some key features that you must look for while selecting a CMMS software:
- Asset Management: Having significant asset information at the tip of your finger is a very helpful feature. It offers you real-time insight into your assets’ health as well as gives you information on how costly they are to maintain and repair. An ideal CMMS software provides asset management feature that offers maintenance logs reports, thereby allowing you to track everything that has been happening with your assets so far (repairs and breakdowns). The software also offers centralized asset card that provides a big picture of everything associated with your asset (view preventative maintenance, work orders, asset information, and logs and reports for a specific asset). Lastly, with asset management, managers get asset hierarchy organization that offers the ability to arrange your assets in a parent-child hierarchy. This is a huge time saver.
- Maintenance Work Management: A maintenance action assigned to an employee is tracked in a CMMS. Almost all maintenance operations can be divided as either PMs, Word Orders, or Work Requests. CMMS software helps in managing maintenance work by offering the ability to set and modify task priority, calendar of upcoming and current tasks, work request portal, automatic work logging, and manage work dashboard. The dashboard shows all critical data such as tasks that are presently in progress, task priority, due dates, and so on.
- Generate and Share Reports: Many times, a company’s maintenance emergencies and problems are brought by a tiny subset of equipment. Viewing historical records of statistics and equipment issues as well as accessing equipment breakdown reports can assist maintenance managers detect problem equipment and fix it. This will reduce equipment breakdown and allow your company to save money and time. In addition to this, the software must make it simpler for upper management to keep the track of maintenance processes by sharing these reports with them through a reporting module. Vital statistics, which will be helpful for the upper management, include pending planned/preventive maintenance, work orders, machine downtime, and more. These reports will assist the management team know the state of your maintenance goals and recognize areas for improvement.
- Preventive Maintenance: A majority of companies are focused on preventive maintenance as it is easier and cheaper to implement. A top CMMS software allows you to run an efficient preventive maintenance program and helps in managing and scheduling all preventive maintenance work. This includes automatic scheduling (based on events, time, or sensor meter readings) and drag and drop calendar that offers a quick overview of all upcoming schedules and open work. Hence, all maintenance technicians get a clear view of which tasks should be performed on priority.
- Spare Parts Inventory Management: It is difficult to operate an efficient maintenance department if you have poor control on spare part inventory. Forcing maintenance employees to repair a part without a replacement in stock is not right. An ideal CMMS software will have features that help you to keep track of and manage your spare parts inventory. In addition to this, the software also offers barcode lookup that provide custom QR codes, thereby giving a simple easy way to access and track your inventory. These solutions also offer annual forecasting for optimizing stock levels. In addition to this, CMMS software also provides instant email and push notifications when quantity of a part reaches set threshold. Lastly, these solutions provide automatic part usage tracking where the inventory is updated automatically to reflect the parts used in the organization.
- Reusable Task Templates: Maintenance managers can design reusable task templates to create work orders easily for routinely occurring tasks. This saves the time spent adding instructions for work orders. In order to design a reusable task template, managers can brainstorm with a maintenance technician to create detailed instructions on how a task must be conducted using best practices. A task template will help new maintenance employees who are not familiar with the task to get up to speed quickly. This helps prevent equipment breakdown and makes sure that the work is done correctly. In simple words, CMMS software allows you to capture the knowledge of your most experienced and best maintenance technicians and save it in your system so that it is available for everybody in your company to use.
- Quick and Easy to Access Work Orders: Maintenance employees are always on the go. Therefore, it can be tricky to keep them updated about the work orders that have been allocated to them. Using the best CMMS software systems can help maintenance technicians access the system anywhere, anytime through cloud. A mobile app makes it possible for maintenance employees to access information about assets and inventory as well as work orders through any smartphone. With mobile app or cloud solution, technicians can also close work orders from a smartphone or a desktop computer. This makes the job of a maintenance managers easier since they do not have to chase after employees to see if they have completed the work. In addition to this, having a simple way to update the work orders’ status frees up maintenance employees and allows them to spend more time on maintenance work.
- Resource and Vendor Management: A good CMMS will help a company with resource and vendor management. The software must be capable of sending work orders or email requests to any resource or vendor in the database of the system. The capability of the system to allocate resources to any on-demand task with a single click will streamline the resource management process of a company. As a part of vendor management, the CMMS solution must be useful in offering maintenance managers instant access to vendor contact details and information.
- Interactive Floor and Site Plans: One of the most essential CMMS features is interactive floor plan management. This lets maintenance managers to interact with assets and equipment in the current floor plan layout. This ability empowers an organization to see where the equipment is, when it needs to be replaced, and when it needs servicing.
-
What are the Different Types of CMMS Software?
-
Analyzing and choosing the top CMMS software can be a difficult task. There are some important features that must be checked for when choosing a CMMS software. The software gathers and stores data about scheduled maintenance and equipment repairs, as well as maintains an inventory of parts and materials. These solutions also keep track of associated costs and handles all related workflows. Here are some key features that you must look for while selecting a CMMS software:
- Asset Management: Having significant asset information at the tip of your finger is a very helpful feature. It offers you real-time insight into your assets’ health as well as gives you information on how costly they are to maintain and repair. An ideal CMMS software provides asset management feature that offers maintenance logs reports, thereby allowing you to track everything that has been happening with your assets so far (repairs and breakdowns). The software also offers centralized asset card that provides a big picture of everything associated with your asset (view preventative maintenance, work orders, asset information, and logs and reports for a specific asset). Lastly, with asset management, managers get asset hierarchy organization that offers the ability to arrange your assets in a parent-child hierarchy. This is a huge time saver.
- Maintenance Work Management: A maintenance action assigned to an employee is tracked in a CMMS. Almost all maintenance operations can be divided as either PMs, Word Orders, or Work Requests. CMMS software helps in managing maintenance work by offering the ability to set and modify task priority, calendar of upcoming and current tasks, work request portal, automatic work logging, and manage work dashboard. The dashboard shows all critical data such as tasks that are presently in progress, task priority, due dates, and so on.
- Generate and Share Reports: Many times, a company’s maintenance emergencies and problems are brought by a tiny subset of equipment. Viewing historical records of statistics and equipment issues as well as accessing equipment breakdown reports can assist maintenance managers detect problem equipment and fix it. This will reduce equipment breakdown and allow your company to save money and time. In addition to this, the software must make it simpler for upper management to keep the track of maintenance processes by sharing these reports with them through a reporting module. Vital statistics, which will be helpful for the upper management, include pending planned/preventive maintenance, work orders, machine downtime, and more. These reports will assist the management team know the state of your maintenance goals and recognize areas for improvement.
- Preventive Maintenance: A majority of companies are focused on preventive maintenance as it is easier and cheaper to implement. A top CMMS software allows you to run an efficient preventive maintenance program and helps in managing and scheduling all preventive maintenance work. This includes automatic scheduling (based on events, time, or sensor meter readings) and drag and drop calendar that offers a quick overview of all upcoming schedules and open work. Hence, all maintenance technicians get a clear view of which tasks should be performed on priority.
- Spare Parts Inventory Management: It is difficult to operate an efficient maintenance department if you have poor control on spare part inventory. Forcing maintenance employees to repair a part without a replacement in stock is not right. An ideal CMMS software will have features that help you to keep track of and manage your spare parts inventory. In addition to this, the software also offers barcode lookup that provide custom QR codes, thereby giving a simple easy way to access and track your inventory. These solutions also offer annual forecasting for optimizing stock levels. In addition to this, CMMS software also provides instant email and push notifications when quantity of a part reaches set threshold. Lastly, these solutions provide automatic part usage tracking where the inventory is updated automatically to reflect the parts used in the organization.
- Reusable Task Templates: Maintenance managers can design reusable task templates to create work orders easily for routinely occurring tasks. This saves the time spent adding instructions for work orders. In order to design a reusable task template, managers can brainstorm with a maintenance technician to create detailed instructions on how a task must be conducted using best practices. A task template will help new maintenance employees who are not familiar with the task to get up to speed quickly. This helps prevent equipment breakdown and makes sure that the work is done correctly. In simple words, CMMS software allows you to capture the knowledge of your most experienced and best maintenance technicians and save it in your system so that it is available for everybody in your company to use.
- Quick and Easy to Access Work Orders: Maintenance employees are always on the go. Therefore, it can be tricky to keep them updated about the work orders that have been allocated to them. Using the best CMMS software systems can help maintenance technicians access the system anywhere, anytime through cloud. A mobile app makes it possible for maintenance employees to access information about assets and inventory as well as work orders through any smartphone. With mobile app or cloud solution, technicians can also close work orders from a smartphone or a desktop computer. This makes the job of a maintenance managers easier since they do not have to chase after employees to see if they have completed the work. In addition to this, having a simple way to update the work orders’ status frees up maintenance employees and allows them to spend more time on maintenance work.
- Resource and Vendor Management: A good CMMS will help a company with resource and vendor management. The software must be capable of sending work orders or email requests to any resource or vendor in the database of the system. The capability of the system to allocate resources to any on-demand task with a single click will streamline the resource management process of a company. As a part of vendor management, the CMMS solution must be useful in offering maintenance managers instant access to vendor contact details and information.
- Interactive Floor and Site Plans: One of the most essential CMMS features is interactive floor plan management. This lets maintenance managers to interact with assets and equipment in the current floor plan layout. This ability empowers an organization to see where the equipment is, when it needs to be replaced, and when it needs servicing.
-
What are the Issues Faced While Using CMMS Software?
-
A computerized maintenance management software is important for efficiently collecting, analyzing, sorting, and acting on vital information associated with facilities and equipment performance. Managers use this data to justify equipment purchases and set department priorities. But in many cases, the software does not offer the expected results, and managers face different challenges in trying to ensure that the tool has the potential to successfully support the company’s mission. These common mistakes can occur when using a CMMS software in your organization. These issues can diminish the productivity, benefits, and cost-effectiveness of using a CMMS, but they are easy to avoid with the correct CMMS. Here are some issues that managers face while using CMMS software:
- Improper Use of the CMMS Software: When used correctly, a CMMS software is a very helpful tool. Using the solution can benefit maintenance planning, asset management, and keep your costs down. On the other hand, if it is not used properly by staff, either due to lack of knowledge or neglect, different issues can arise. It is often seen that CMMS gets user-generated problems such as entering inconsistent data, forgetting to input data, or not performing the continuous asset maintenance checks notified by the CMMS solution. These apparently small user errors can overlap and result in even bigger problems moving forward, thereby costing organizations both money and time. Always remember, a CMMS software is not only about the solution itself, but also the way users feed the data to the system and use the information it offers.
- Implementation and Training: Another common issue faced while using CMMS software is little or no prior experience with the software or lack of knowledge regarding maintenance. Training and implementation task must be allocated to a team or individual with a high level of knowledge, which will allow them to evaluate the complete asset inventory and set up the correct support for every asset. A lack of proper training for all maintenance employees can lead to many issues. If a team member is not given clear instructions, they are expected to apply their own methods and strategies while using the software, lead to a chaotic and confusing set of asset data.
- Task Management Failure: Some managers might neglect to allocate specific roles for every member of the maintenance management team or might not properly define the requirements and expectations for these roles. Be certain to make these definitions clear in your software to avoid mix-up about who does what and when, which can result in costly mistakes. Moreover, it is essential to ensure that both upper and middle management are able to use and understand the solution. This will help guarantee that asset management tasks are correctly delegated and each team member is responsible for their role in the organization.
- Time and Resources: The more assets you own, the more time and resources you will need to spend on maintenance. Maintenance management must be an incessant process, meaning team members must commit daily hours to ensure smooth operations. In this manner, the company will help ensure all maintenance objectives are achieved, helping to grow rather than hampering the company’s success.
-
What are the Benefits of CMMS Solutions?
-
The benefits of CMMS software are abundant and here are few for your reference:
- Manage Maintenance Backlog: Some amount of maintenance backlog is inevitable, but too much can set you operations back. As per a study, the cost of backlogged maintenance globally is predicted to be $12 Billion. This illustrates the significance of keeping maintenance backlog at an adequate level. A CMMS software balances maintenance costs and resources, and therefore backlog does not get out of control. The software detects small errors and mistakes that would otherwise go unnoticed and allows maintenance tasks to be scheduled, allocated, and prioritized so no operations are left unnoticed.
- Increased Reliability of Aging Assets: Age is not always the reason for equipment or machinery failure. But it is often a contributing factor. It is not always financially conceivable to replace old tools with a new one, which is why maintenance is so essential. CMMS software offers a way to gather, evaluate, and use an asset’s historical information. This data makes it simpler to see trends in performance of an asset and decide on the frequency and type of maintenance for an asset. This guarantees that aging tools are as healthy as possible.
- Enhanced Preventive Maintenance: Preventive maintenance identifies defects before they turn out to be a bigger issue, thereby lowering the odds of breakdowns. Maintenance teams is aware that preventive maintenance is key to reducing downtime, but the actual question is, how do you schedule and manage preventive maintenance? CMMS software solves this issue by automating work orders. Preventive maintenance triggers can be generated based on time, usage, or condition in the software. These triggers activate a work order, which is then scheduled and allocated. The work order turns out to be much smoother and preventive maintenance is simpler to schedule, resulting in less downtime.
- Easy Repairs and Inspections: Downtime takes place whenever an asset requires to be inspected or repaired. This is not always avoidable. On the other hand, if preventive maintenance and repairs are inefficient, it increases the downtime. These inefficiencies can add up and cost your company a lot of money and time in lost production. Computerized maintenance management software makes it simpler to inspect and repair assets, and hence downtime is reduced to the bare minimum. The solution makes it possible for technicians to log into a mobile app and see an asset’s the location of spare parts, diagrams, history, and more so the job can get performed quickly.
- Enhanced Inventory Control: Not having a management on inventory can result in all kinds of expensive issues. As per a study, overspending on inventory can add an extra 12–20% to the initial purchase cost. If you do not have the correct parts on-hand when tools break down (or you cannot find the parts in an unorganized storeroom), it leads to rush shipping, downtime, and risky stopgap measures, all of which are costly. Handling your inventory using a CMMS software helps you buy, organize, and track parts so you can avoid these expensive issues. Features, such as inventory reporting and automated purchasing, can assist you make data-based inventory decisions and get rid of under- and overstocking.
- Avoid Production Scrap and Rework: Both rework and scrap need a huge cost in the form of waste, energy, and lost production. In addition to this, it is very difficult to make up for that expense without the manufacturing team doing overtime. The best way to limit the cost of rework and scrap is to avoid unplanned failure by using preventive maintenance to keep assets healthy. CMMS solutions excels at helping maintenance teams schedule, plan, and execute preventive maintenance. CMMS not only automates tasks, but also prioritizes and assigns preventive maintenance while tracking major metrics to optimize it.
- Maintenance Costs Management: CMMS software tracks everything related to completed work orders, including labor, parts, and other costs. This makes it simple to create a report on these costs, analyze where the budget was spent, and make educated replace or repair decisions. If you are looking to prove the worth of maintenance, you can even evaluate the cost of planned and reactive maintenance.
- Save Energy: As per a study, manufacturers spend $230 billion on energy annually, which means that any company can limit costs by lowering the use of energy. Well-maintained assets are more energy-saving and are essential in reducing your overall energy costs. Unplanned maintenance is a primary source of wasted energy at manufacturing facilities since it leads to poor scheduling, inventory issues, rework, and more. A CMMS solution can solve each one of these problems by helping you establish an enhanced preventive maintenance strategy with features such as easier work scheduling and automated work orders.
- Enhanced Maintenance Schedule: Well-planned maintenance schedules waste less resources, time, and money. Enhanced planning is possible when you can anticipate every component of maintenance, such as production schedules, asset needs, and inventory. Creating a better maintenance schedule begins with knowing your resources and your assets. A CMMS helps you do this by collecting, tracking, and studying data from performance of an asset. From here, you can modify the frequency of preventive maintenance tasks and make sure that your maintenance schedule employs staff resources as efficiently as possible.
- Automated Work Requests: It is common for maintenance managers to get work requests via whiteboard, sticky notes, phone, or verbally, but none of those are ideal. These obsolete processes force maintenance teams to spend unnecessary time generating work orders and adding data. CMMS solutions eliminate all the additional steps by automating the process of work request. Employees can set up PM triggers, log work requests, or connect to sensors that generate work orders on the basis of an asset’s real-time condition. No time is wasted tracking down operators, translating work orders, or rifling through a file cabinet.
- Improve Access: A lack of centralized knowledge indicates shuffling through stacks of paper, having to track someone down, or searching via a PC to find the fix to a breakdown. These little inadequacies result in bigger problems, such as failed audits and more downtime. A CMMS makes resources available readily to anybody, at any time by offering a centralized hub for data. Attach manuals, videos, inventory requirements, accident reports, task lists, and more to any piece of work order or equipment to assist technicians get tasks done in minimum time.
- Track Maintenance Metrics: Maintenance metrics convert action into figures so you can calculate the performance of everything and everyone in your operation. They let you to link cause and effect so you can improve your operation by making better decisions. You cannot track metrics without the correct processes, tools, and people. CMMS solution is the right tool to be used for this calculation. It studies the figures and tracks metrics over time so you can see the big picture of your performance. It also makes it simpler to study the metrics and modify strategies based on the data.
- Report on Relevant KPIs: Maintenance KPIs assist you recognize chronic equipment issues and benchmark against industry standards. On the other hand, compiling KPI reports with pen and paper or Excel can be monotonous and result in mistakes. CMMS tools allow you to gather data from different areas of your maintenance process and make them insightful using reporting templates. Having a better knowledge of your KPIs helps you reduce risk or add value with small changes. You can quickly track costs, spot recurring problems, analyze trends, and more.
- Regular Updates on Processes: Being able to keep a track of the progress of work orders is essential for creating effective schedules, reducing backlog, building budgets, and planning production. If the right people do not have visibility into work orders, it results in higher costs, more downtime, and uninformed decision-making. A CMMS software helps you prevent these issues and offers real-time work order updates, such as who is assigned to the task, the priority status, and how long it is taking. In this way, you can assign additional resources if required. The CMMS also alerts production staff when assets are back online, so they can get start working without any wastage of time.
- Access Historical Data: It’s tricky to manage an asset through its complete lifecycle if you do not know its history. Even if your employees know everything about an asset such as when it was purchased, how often it is used, what were the issues faced by it, and so on, that doesn’t guarantee the access of data. A CMMS tool offers a defense against this kind of brain-drain. Every asset has its own record that shows everything that has been done to it, from inspections to repairs, labor hours, and so on. Employees can access these records quickly to help with preventive maintenance or troubleshooting a failure.
- Job Safety: How quickly the job is performed doesn’t matter, rather how safely and efficiently it is performed matters. The odds of an accident elevate when safety is not part of the planning process. Making sure each job is safe adds a few additional steps when generating a work order, but it is well worth it to keep your team safe. A CMMS tool makes it simpler to generate work orders that have the security of the maintenance team in mind. You can add safety procedures, material safety data sheets, checklists, and essential PPE so you can be certain that employees are avoiding risks and doing a job safely.
- Audit Preparation: Audits are not always easy to pass and it is even harder without the correct knowledge and tools. In addition to this, the prospect of failing an audit brings a huge headache with it along with the risk of losing millions of dollars. CMMS tools make it more cost-effective and easier to get ready for an audit. It helps simplify inspection rounds and makes it possible to search the system for maintenance records for a specific time period or of a specific asset. Documenting compliance tasks is also easier with the software as it offers you the opportunity to store photos and create reports.
- Eliminate Violations and Penalties: Safety violations result in more accidents and can take a toll on the success of a company, costing the business millions of dollars in penalties. These violations often take place when expectations aren’t clear, people are missing information, and communication breaks down. A CMMS tool can be a fixture to these problems. Safety procedures can be made more visible and accessible on asset profiles and checklists. Employees can pull up these procedures on their smartphones within seconds so they never miss vital safety instructions that could result in a violation.
- Safety Training Management: Training is a major element of safety. As per a study, it has been observed that safety training reduces the chances of injuries by 24%. It also results in fewer breakdowns and unpredicted costs. Even though safety training is essential, everything from the need for specialized skills to bad timing can hamper your team’s best-laid schedules and plans. CMMS tools can help eliminate the obstacles by a safety training. The software allows you to save and track safety and health information for technicians, such as certifications. You can also get safety reports from the solution so you can decide what sort of training should be prioritized.
-
What are the Trends in CMMS Software?
-
As existing technologies improve and new innovations come into picture, the maintenance management industry will continue to thrive and grow. The demand for faster, better, and more secure CMMS software is on rise and sufficed by emerging trends. Here is a list of trends that will be seen in the future:
- Mobility: Agile business strategy plays a major role when it comes to reliability and maintenance. Technicians need a technology to match their speed and mobile app is helping them in doing so. These apps can make technicians almost 15–25% more productive, as per a study. When technicians can do everything from getting work orders in the field, to analyzing the history of work order, productivity increases. A mobile app can also make a technician’s smartphone into his own mobile office. When you can access necessary data over your mobile app from the cloud, there is no need to actually be present at the office. A CMMS software with a mobile app can also save data entry costs. Instead of transporting completed work orders back to the office, technicians can just click “done” on their tablet after ending a job.
- Industrial Internet of Things (IIoT): The IIoT is a catch-all phrase for internet-based manufacturing tools. The equipment is integrated with sensors that offer performance data to the CMMS solution. The technology has also been a huge trend for the past few years. IIoT could create a huge amount of money for the world’s economy in the future. Top benefits of the technology are increased revenue as well as customer satisfaction. Hence, IIoT is one of the upcoming trends that will be seen becoming mainstream in the coming years.
- Predictive Maintenance: One of the many objectives of any best CMMS software systems is to lower downtime. Predictive maintenance uses real-time, sophisticated measurements to determine when an asset may require a fix, and make that objective a reality. In preventative maintenance, technicians look at an equipment’s history to predict when it may break. On the other hand, predictive maintenance uses techniques such as machine learning algorithms to make its forecasts. The shift to predictive maintenance can be made smoother using a CMMS tool. Hence, predictive maintenance is the future of CMMS and will soon become mainstream in the future.
- Artificial Intelligence and Internet of Things: Smart and connected tools are the future of the industry. As such, the IoT and AI are trending topics in the industry. When our machines are smart, they can evaluate themselves and send real-time information back to managers, thereby preventing a number of unexpected failures. Organizations are dramatically augmenting the use of IoT and using that information to support asset and maintenance management plans. From analytics and predictive maintenance for real-time asset management decisions, CMMS software will offer managers a more vanguard position at the table. The goal of elevated IoT autonomy and integration is to gather more information as well as insightful data. This offers users the power to make data-driven decisions that comply with long-term objectives. IoT and AI will align together with CMMS software to become more sophisticated in real-time applications.
- Cloud Computing: Cloud computing lets consumers to access the CMMS from anywhere through the Internet since the data, software, and/or hardware are hosted outside your organization. Cloud computing is dependent on interoperability standards and lowers costly interfaces between databases and applications. This in turn leads to better decision-making and greater efficiencies. Thus, users must care about cloud computing as a means of more quickly and easily accessing the latest version of CMMS solutions and all of the needed data irrespective of source.
- Proactive Maintenance: Unexpected outages, comprising those caused by global crises and pandemics, can threaten a company’s ability to maintain assets properly. Downtime related to unexpected outages can be very costly, leading to increased labor costs and production shortfalls. Equipment failure can also result in dangerous breakdowns and safety hazards. This can lead to a rise in potential dangers related to unexpected outages. During a serious breakdown, company resources and employees can be at a great risk. Proactive management of industrial maintenance will take over passive, traditional maintenance solutions. A proactive strategy predicts and resolves underlying maintenance issues before they can happen. This is of significant importance as it guarantees all equipment works at peak performance levels, reducing labor and maintenance costs as well as dramatically lowering the odds of unplanned outages.
5G: Over the coming years, 5G is predicted to be one of the most disruptive technologies in the market, becoming the cornerstone of a new data-based ecosystem all over different vertical sectors such as oil and gas, manufacturing, education, and healthcare. The possibilities of 5G will enable for data-rich environments, machine-enhanced decision-making, intelligent efficiency, agile automation, and trusted connections. These enhancements in the CMMS industry will dramatically enhance safety, productivity, and efficiency. As 5G is capable of connecting everybody to everything and everywhere, companies that use CMMS solutions can expect to derive value from this new connected ecosystem. 5G technology will improve responsiveness to increase asset and maintenance management efficiencies. This has an overall effect on revenue figures and can act as a potential driver for business development. The improved connectivity of 5G will enhance output and guarantee proactive maintenance measures are supported by emerging technologies such as data analytics and IoT. This allows companies to collect smart data insights to make informed decisions.
-
How Much Does CMMS Solutions Cost?
-
The average cost of a computerized maintenance management software will vary depending on your deployment selection and vendor. The number of resources that will be employing the system and the features you want will impact the cost as well. Typical pricing plans are as follows:
- Subscription Plan by Month Only: Bigger organizations that need many users to access a CMMS tool might choose this subscription model. Normally, a vendor will specify level of features and maximum number of users. On the other hand, some unlimited user plans are also available. Configurations and price range vary widely. Packages might specify access to particular features, number of users, number of sites, and so forth.
- Subscription Plan by User and Month: This subscription model is developed for smaller organizations with low number of users. Organizations are charged only for the actual number of users who use the software in a given month. These tools are deployed via the cloud and allow easy mobile access for field workers. The price can start as low as $5 per month per user for basic features. High-end plan might be around $50 per month per user for whole management access with analytics features.
- Perpetual Licensing Fee: Companies that have a large number of users and need customizations in CMMS might need to invest in a perpetual license. This is normally paid upfront, is significantly expensive than other subscription models, and includes an unlimited number of users and sites. Future software upgrades, on the other hand, usually cost more.
-
Why Purchase CMMS Software from WareBuy?
-
WareBuy is the industry’s first dedicated marketplace for buying and selling packaged software solutions and services. Buying a software will be easy since the platform offers different benefits such as:
- Secured payment
- Multiple options for software
- Price Transparency; hence, no additional or hidden costs are added to the cart.
- 24/7 customer support
- Saves time
- Worldwide delivery
- Competitive pricing
- Shop by category (such as industry or skillset)
- Buy products from renowned brands
We would love to hear from you. For any doubts, please contact us here.